Advanced Automatic 5 Gallon Water Filling Machine for High-Volume Bottling
In today’s rapidly developing bottled water industry, the 5-gallon water filling machine has become a key piece of equipment for efficient production. This automated filling machine is designed specifically for filling mineral water, distilled water, and purified water, catering to a variety of needs from small businesses to large production lines. With its 304 stainless steel construction and advanced electronic and pneumatic components, the 5-gallon water filling machine not only ensures a production capacity of up to 900-1500 bottles per hour but also features precise filling volume control and automatic cleaning functions, significantly enhancing production efficiency and product quality. Choosing the right 5-gallon water filling machine can not only boost a company’s production capacity but also meet the increasing market demand.
Specifications
Main configuration | Technical parameters |
Filling pump | CDMF32-3 5.5KW |
Cylinder | SU63*350 |
Cylinder | SU63*50 |
Low-voltage electrical components | AC contactor, relay, etc. |
Mechanical filling valve | Variable frequency speed control pneumatic |
Inverter | FR-E740-2.2K-GHT |
Installed power | 10KW |
Dimensions | 3800(L)×1500(W)×2400(H)mm |
Material description | Bracket: 2mm316 stainless steel stamping plate folding
Side panel: 3mm316 stainless steel stamping plate folding Water tray: 2mm316 stainless steel |
Video
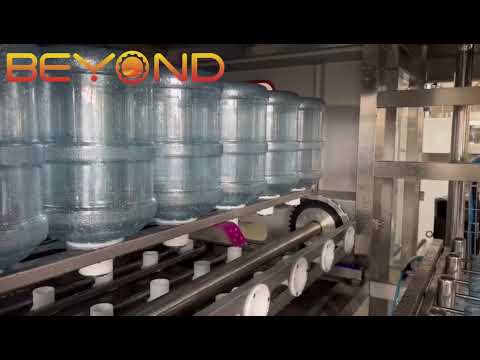
Description
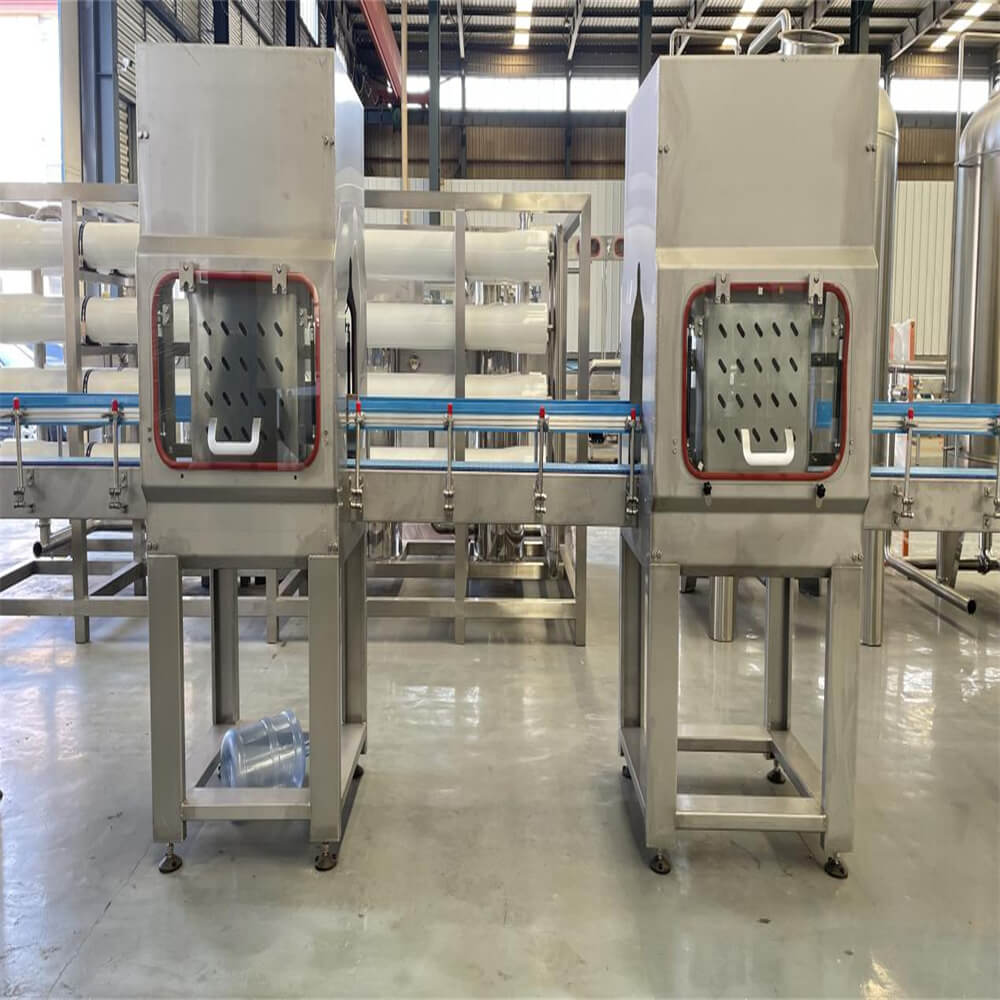
The automatic capping machine performs a swift and precise uncapping process in less than 4 seconds:
- Cap Grabbing: The piston of a square cylinder in the uncapping head moves upward, activating a conical block and two claws to firmly grip the barrel cap.
- Cap Removal: The uncapping head’s piston lifts the barrel while a fixed baffle blocks the barrel’s shoulder, effectively pulling the cap off.
- Cap Release: The square cylinder piston moves downward, spreading the claws to release the cap, which drops under its weight.
- Cap Blowing: Compressed air from the nozzle blows the cap to the collection box.
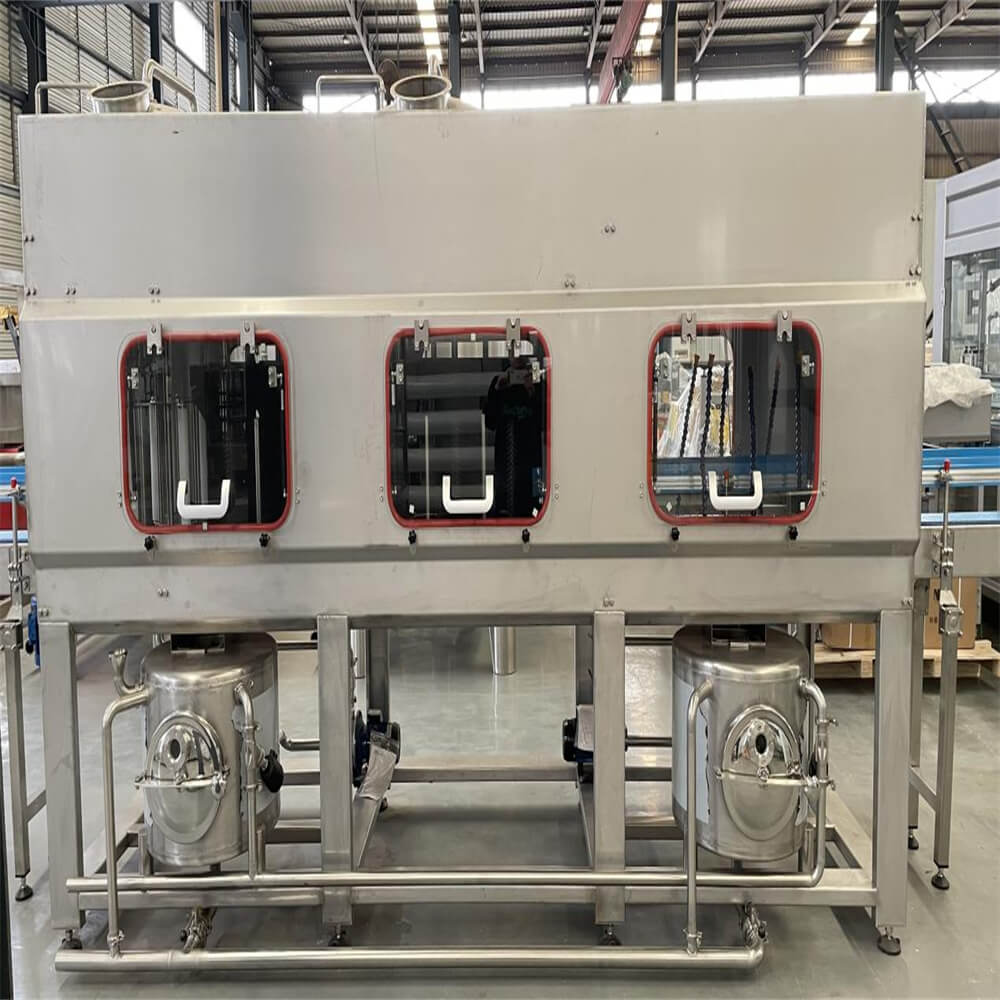
The linear external barrel washing machine ensures efficient and thorough cleaning of barrels with the following features:
- Structural Composition: It includes a frame, washing water/alkali solution circulation system, clean water flushing system, transmission system, filter, plexiglass cover, mechanical conveyor, and electrical system.
- Efficient Cleaning: Streamlined online operations remove oil, mosquitoes, fibers, and other debris, ensuring the barrel’s outer wall is completely clean. Residual water inside the barrel does not exceed 20ml after pre-washing.
- High-Quality Components: Equipped with a reliable Nanfang pump for clean water flushing.
- Durable Transmission System: Made of high-strength, wear-resistant, and corrosion-resistant materials, with a clutch to prevent barrel jams or damage, ensuring stable and reliable performance.
This barrel washing machine delivers effective cleaning for a range of industrial applications.
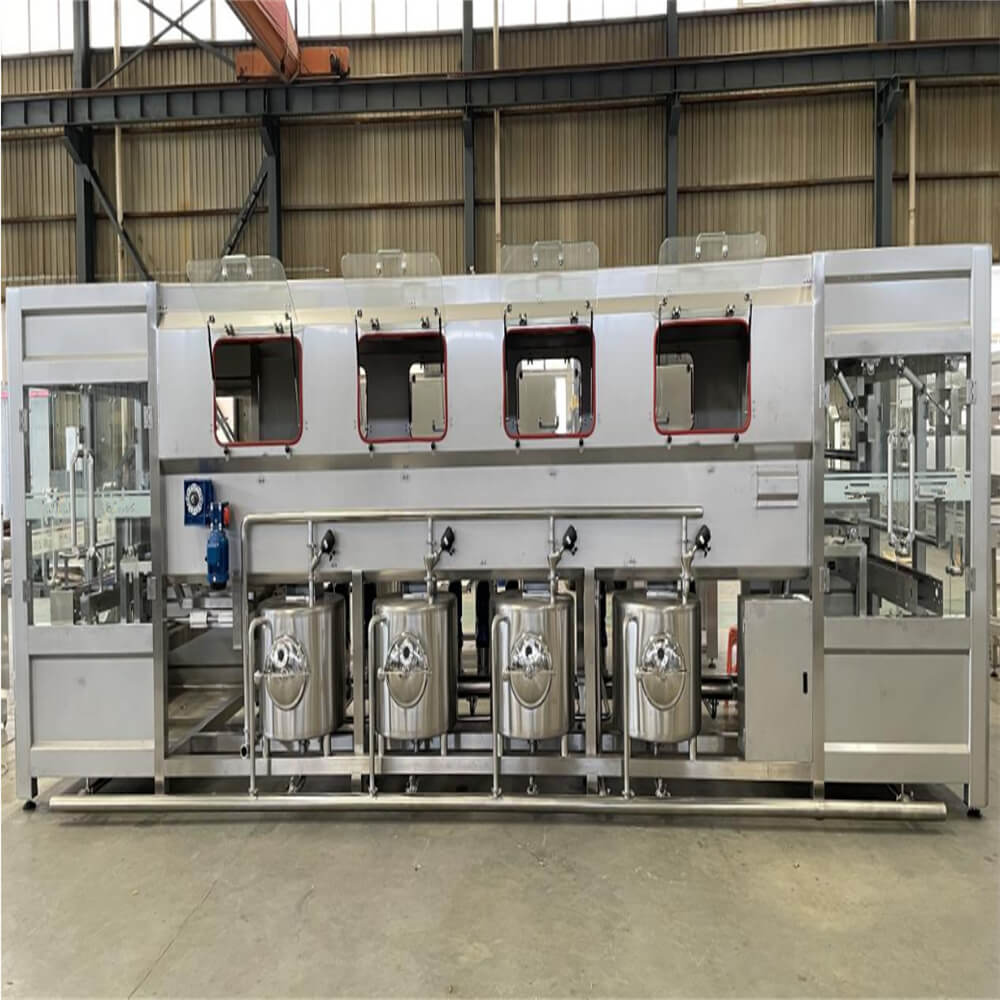
The internal flush machine and barrel washing machine are designed for effective barrel cleaning with the following features:
- Structural Composition: Includes a sturdy frame, automatic upper and lower barrel system, forward mechanism, sterile water return, disinfectant and water circulation spray systems, reducer transmission, and electrical components.
- Automatic Upper and Lower Barrel System: Cylinder flip mechanism ensures precise handling without barrel wear. Two flip cylinders made from durable Korean APT material enhance thrust. The frame uses thick-walled square tubes (≥2.0mm) to prevent weld fractures and deformation.
- Flushing Liquid Circulation System: Sterile water, return water, and disinfectant are sprayed uniformly at high pressure using all-round nozzles, thoroughly cleaning the entire barrel’s inner wall.
- Convenient Maintenance: Circulation boxes feature liquid level displays, conical disinfectant tanks, filling covers, manholes, and replaceable stainless steel filters (0.22µm) for effective water filtration and easy cleaning.
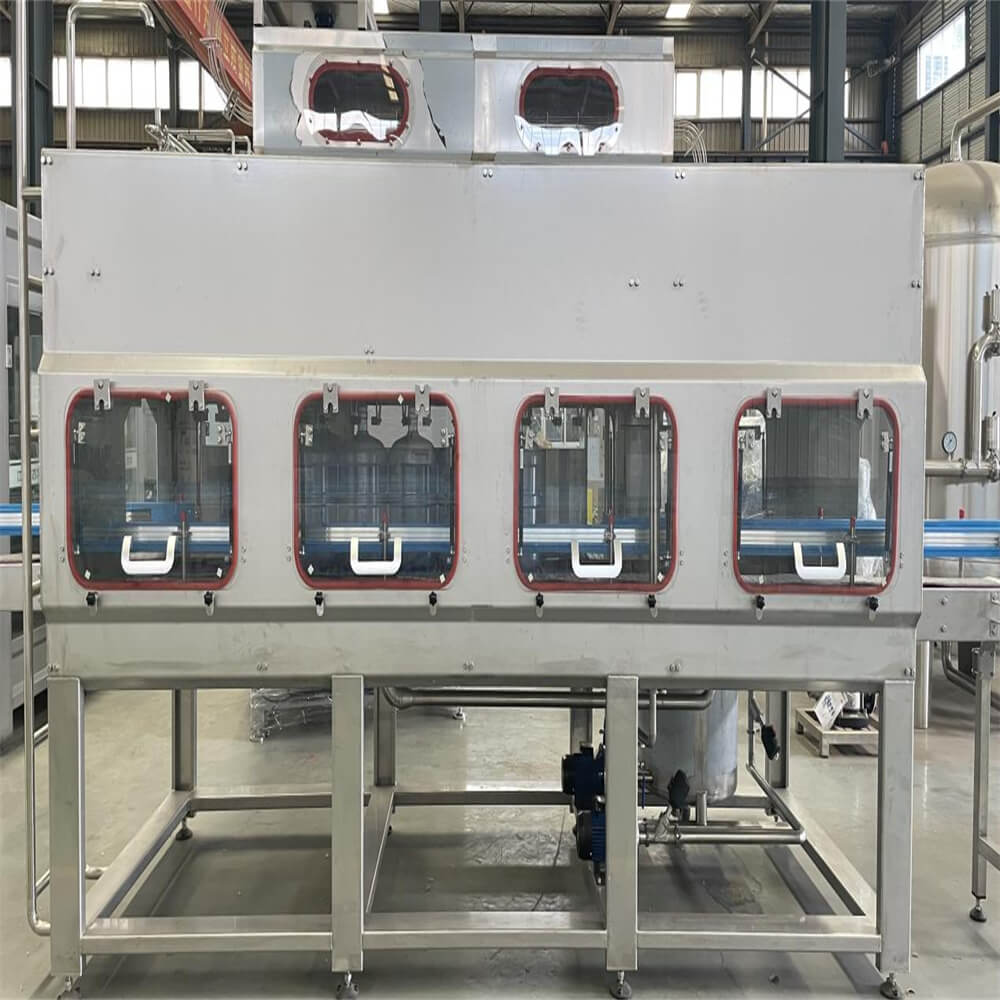
The linear filling machine and liquid filling machine are designed for precise and efficient liquid filling operations with the following key features:
- Structural Composition: Includes a robust frame, power transmission system, high-flow filling mechanism, mechanical conveying, and a central control system for seamless operation.
- Advanced Filling Process: Utilizes non-contact bottle mouth filling with a large-flow filling valve and variable frequency water pump, minimizing water loss and ensuring accurate liquid levels.
- Lifting, Sorting, and Sealing System: Features a cap storage box, rotary cap sorter, and a stainless steel chain for continuous and reliable capping.
- Technical Excellence: Equipped with 8 filling valves for shift filling to meet high-speed requirements. A unique guide rail filling method reduces maintenance costs, ensures operational stability, and achieves optimal filling results.
- Reliable Power Transmission: Smooth, stable, and easily maintained transmission components ensure long-term durability.
- Filling Mechanism: Incorporates a sliding seal filling valve core for enhanced precision and performance.

The automated disinfection system and automatic lidding machine streamline barrel cap handling and ensure hygienic operations with these features:
- Efficient Cap Feeding: Barrel caps are fed in batches by the cap feeding machine and sorted quantitatively on the cap sorting plate for organized processing.
- Automatic Disinfection: Caps are transferred to the cap washing position for fully automatic disinfection and rinsing, ensuring hygienic standards.
- Hygienic Flushing: Finished product water rinse removes residual chlorine for enhanced cleanliness.
- Accurate Cap Pressing: Crawler-type cap pressing ensures uniform force and precision, maintaining consistent product quality.
- Durable Construction: Features a new laser-cut stainless steel cap sorting plate and sliding trough for long-lasting performance.
- Smart Cap Sorting: Automatically corrects reversed caps and halts operations when caps are full, optimizing efficiency.
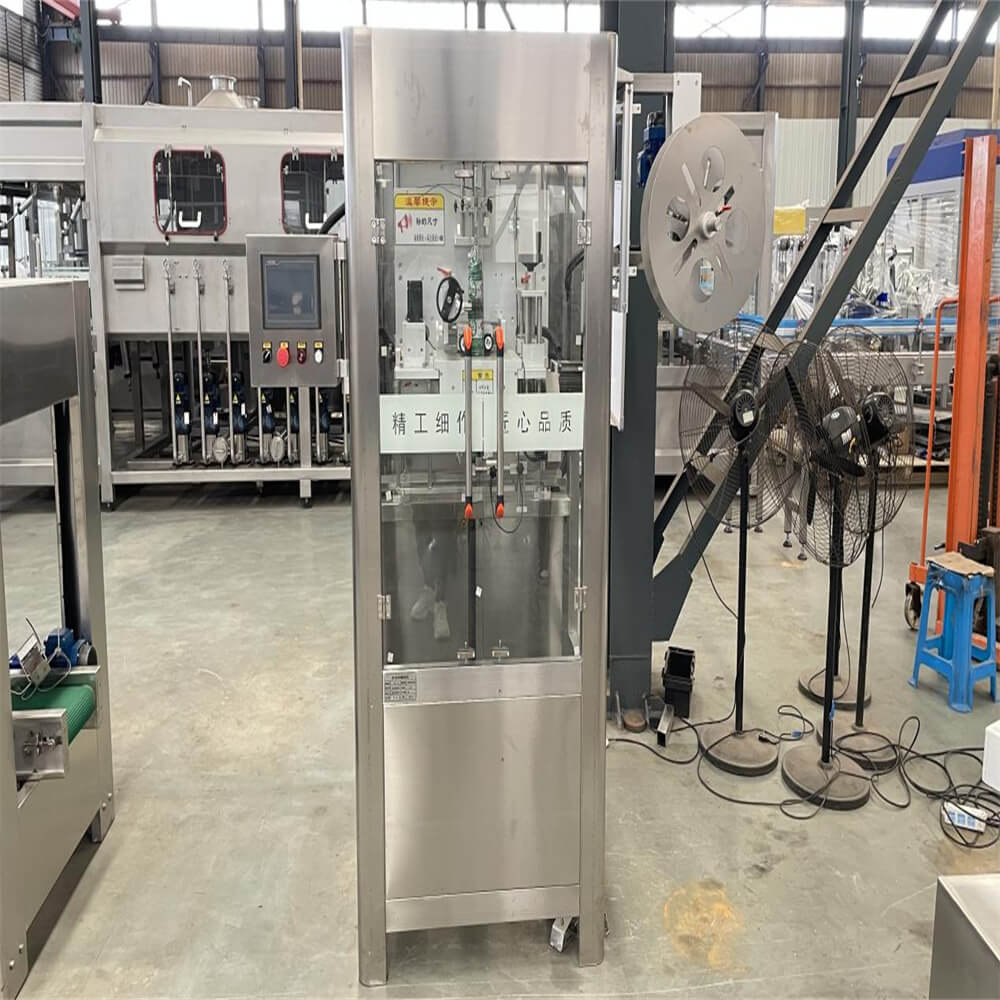
The automatic sleeve labeling machine ensures precise and efficient labeling with the following working principle and components:
Working Principle
The barrel enters the labeling system, and the labeling electric eye detects its arrival, sending information to the PLC control center. The PLC issues four sequential instructions: label delivery, positioning, label cutting, and label shooting. Once label shooting is complete, the barrel moves to the label sorting and shrinking unit, completing the labeling process.
Key Components
- Labeling Host: Drives the roll of labels, cuts individual labels, and places them on the product. Includes a servo motor, label delivery and shooting wheels, cutting box, film guide cylinder, and synchronous label shooting mechanism.
- Pre-Loose Film Device: Supplies label film with consistent tension using a motor, loose film sensor, and swing arm tension mechanism.
- Label Shifting Device: Moves the label film to the lower part of the product using a motor and nylon strip.
- Power Control: Manages the main power switch and controls label sleeve and heat shrink functions separately.
- Human-Machine Interface: Enables program automation, separate action control, and storage of operation parameters for efficient and customizable labeling.
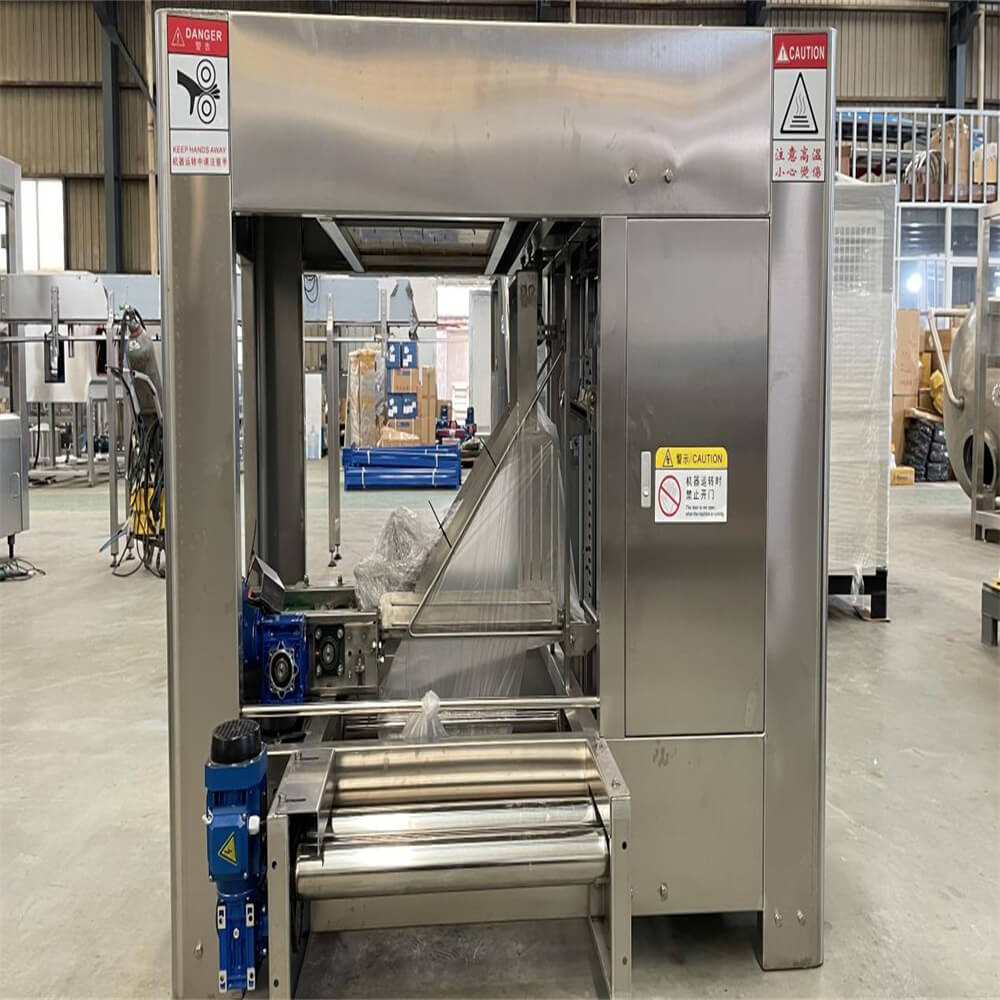
The bagging machine and fully automatic bagging machine are designed for efficient and automated packaging with the following features and working principles:
Key Components
- Frame Mechanism: Provides fixed installation for all operational mechanisms.
- Bottle Conveying Mechanism: Transports items to be packaged.
- Bottle Separation Mechanism: Ensures proper spacing and travel control for packaging items.
- Bottle Pushing and Guiding Mechanism: Positions items at the sealing and cutting station.
- Film Feeding and Conveying Mechanism: Supplies packaging film seamlessly.
- Film Heat Sealing and Cutting Mechanism: Handles precise sealing and cutting for film application.
- Electronic Control System: Manages automatic operations via programmed controls.
How It Works
The barrels are transported to the packaging area by the conveying mechanism. A photoelectric detection head signals the conveyor to stop, initiating the bottle pushing mechanism to guide items along with the film to the sealing and cutting position. Simultaneously, the film feeding mechanism supplies new film, and the heat sealing cutter seals and cuts the film, completing the packaging process. The packaged item is then transported out by a conveyor belt, ensuring continuous and fully automated operations.
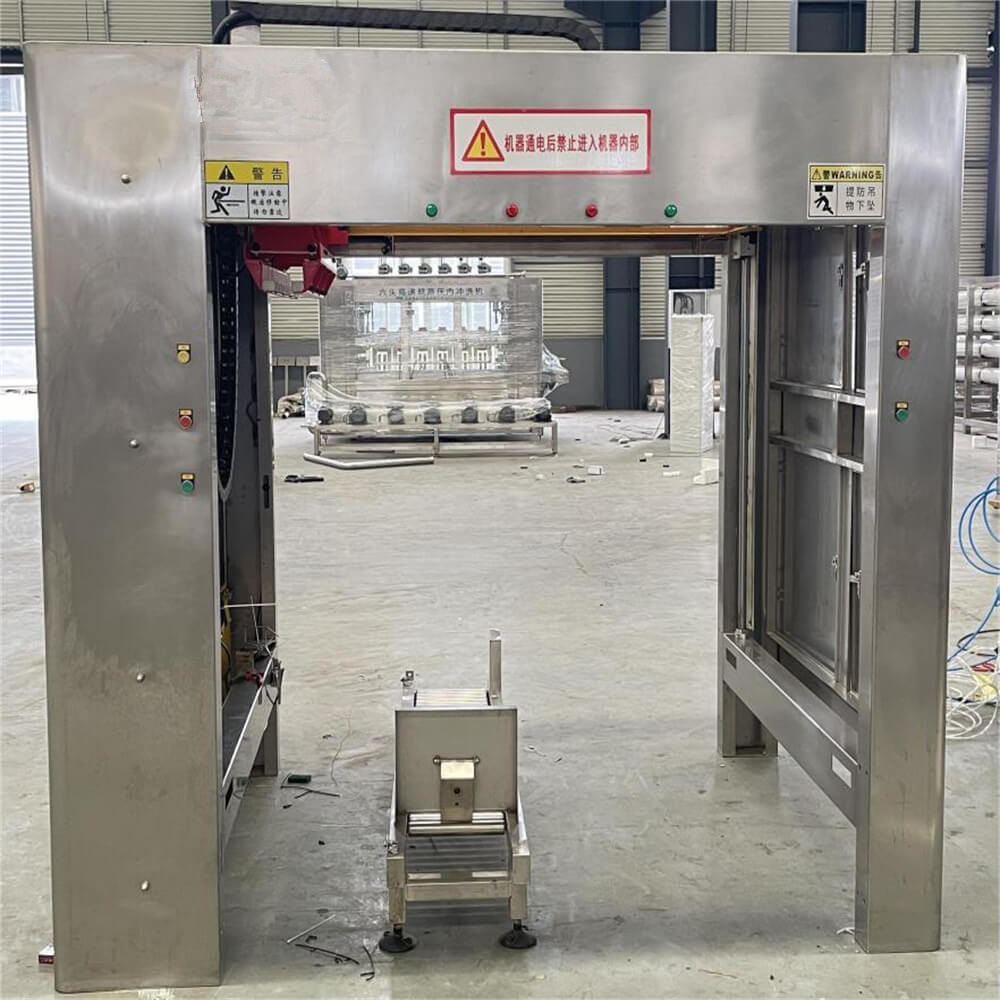
The gantry palletizer and gantry palletizer system provide fully automated palletizing solutions for efficient production processes:
Key Features
- Automatic Control: Handles pallet picking, placing, barrel feeding, barrel grabbing, partition placement, and pallet unloading entirely automatically.
- Customizable Arrangements: The system arranges barrels into 4 rows (4 barrels per row, customizable based on customer requirements) using a pneumatic mechanism for precise alignment.
- Seamless Palletizing Process: The barrel grabbing mechanism lifts and places water barrels onto the pallet layer by layer. After stacking a layer, partitions can be manually placed, followed by subsequent layers.
- Automated Pallet Unloading: Completed pallets are automatically unloaded for removal via forklift, ensuring uninterrupted operations.
Working Principle
The process starts with manual placement of an empty pallet at the designated position. Barrels are bagged and transported via conveyor to the palletizing area. The gantry palletizer system arranges and stacks the barrels efficiently, adding partitions as required. Once stacking is complete, the pallet is automatically unloaded, and the cycle continues with a new pallet.