Choosing the right labeling machine can significantly impact production efficiency and operational costs. Hot melt glue labeling machines, also known as hot melt glue machines, save 30-50% in material costs by using eco-friendly hot melt glue films and minimizing adhesive consumption with advanced application techniques. These machines can label over 30,000 bottles per hour with full automation, reducing downtime and labor costs.
Compared to automatic sticker labeling machines or bottle sticker labeling machines, hot melt machines deliver superior long-term savings and require less maintenance. While shrink sleeve machines are ideal as water bottle labeling machines, their reliance on heat-shrink processes increases energy costs and risks label deformation. For businesses seeking scalable, sustainable, and efficient solutions, hot melt glue labeling machines for bottles provide optimal performance and significant long-term cost savings.
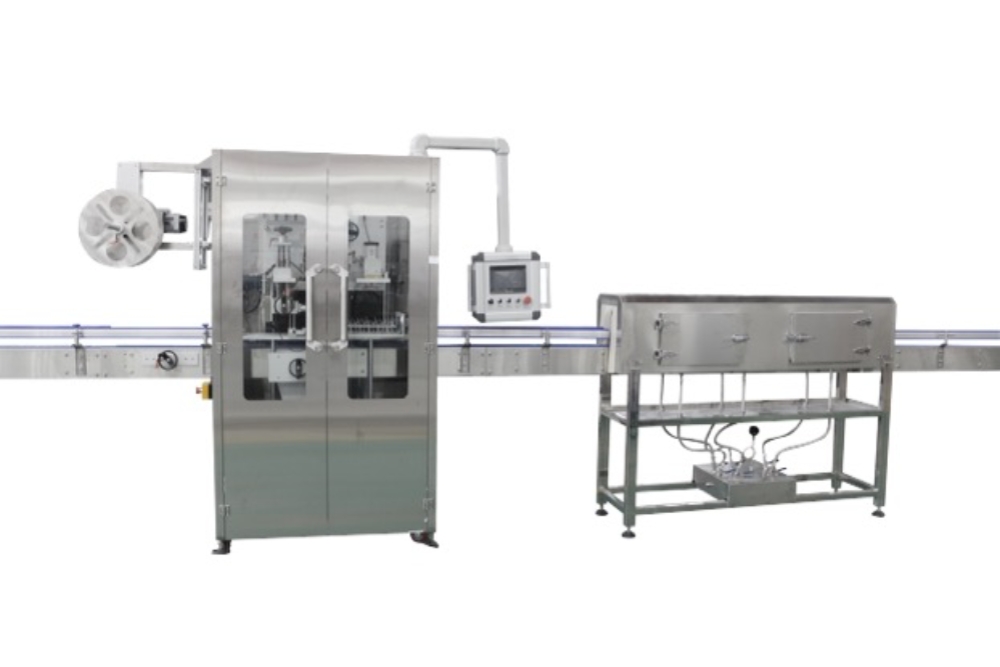
Tables: Performance, Cost, and Applicability Comparison
Table 1: Comparison of Labeling Technology and Efficiency
Aspect | Hot Melt Glue Labeling Machine | Traditional Self-Adhesive Labeling Machine | Shrink Sleeve Labeling Machine |
---|---|---|---|
Labeling Technology | Uses hot melt glue film with advanced adhesive application | Uses self-adhesive labels, typically paper or foil | Uses shrink sleeves that adhere through heat-shrink |
Advantages & Disadvantages | Maintains label shape, suitable for various container shapes (round, square, oval) | Labels may peel or deform in high temperature or humidity | Shrink sleeves may deform after shrinking, affecting aesthetics; suitable mainly for round containers |
Production Speed | Over 30,000 bottles per hour with full automation | Slower speed, requires manual intervention | Suitable for high-volume production but requires heat shrink equipment, increasing energy consumption |
Energy Efficiency | Automated design saves labor and improves efficiency | Low efficiency with bottlenecks in multi-task operations | Requires heat shrink tunnels, increasing energy consumption |
Table 2: Comparison of Costs and Applicability
Aspect | Hot Melt Glue Labeling Machine | Traditional Self-Adhesive Labeling Machine | Shrink Sleeve Labeling Machine |
---|---|---|---|
Primary Cost | Hot Melt Glue Film & Adhesive: Saves 30-50% in material cost; minimal glue usage applied only at the ends | Label Material & Labor: Frequent material changes and manual intervention increase costs | Shrink Sleeves & Heat Shrink Equipment: Higher material and equipment costs, with increased energy consumption |
Cost Efficiency | Environmentally friendly materials lower long-term operating costs | Low initial investment, but higher long-term operational costs | High energy usage leads to increased operational costs |
Applicability | Suitable for beverages, food, cosmetics, and various container types | Primarily used for food, pharmaceuticals, and chemicals but with limited container adaptability | Mainly used in the beverage industry, ideal for bottled water and soft drinks |
Summary | Increases efficiency, reduces long-term costs, and offers flexibility | Limited adaptability and higher operational costs | High material and energy costs, with deformation issues limiting broader applications |
Summary:
Choosing Hot Melt Glue Labeling Machines offers significant savings of 30-50% in material costs and reduced glue consumption through advanced application techniques. The automated system enhances production efficiency while lowering labor costs. In comparison, traditional self-adhesive labeling machines may have a lower initial investment, but frequent material changes and manual intervention lead to higher long-term operational costs. Shrink sleeve labeling machines are useful for specific industries like beverages but have higher operational costs and risk of deformation, affecting aesthetics.